Search
- 12/02/2021
Case Study | USI Develops 5G mmWave Module Reliability Testing System to Raise 85% Testing Efficiency
5G mmWave modules are brand new and must-have components for your future 5G smartphone devices. However, the design is much more challenging and complex than that of 4G but the benefits are worth it: increased of the chip efficiency, the framework and the system design. Nevertheless, a solid product test and a verification process are required to ensure a high-quality product in the design phase.
Thereby, it requires a considerable number of resources such as workforce, material and equipment. We found it’s more complicated than ever before and must sort out a more efficient testing solution to enable mass production faster. Therefore, we came up with a new testing method for the 5G mmWave modules which provides accurate and time-efficient to optimize the testing efficiency and enter the mass production faster.In the reliability verification test,
the 5G mmWave module requires more time for calibration and measurement.
The module needs to be monitored in the designed testing mode
for a minimum of 1,000 hours.
Simplified Testing
Conventionally, when we run a test, the DUT (Device Under Test) is mounted (SMT) on an evaluation board (EVB). We can find each tested module’s location on the EVB through scanning its exclusive barcode. Once completing the testing, the EVB will be scrapped. The reliability testing usually involves a simulation where the product is put under the extreme conditions like high temperature or high humidity environment for an extended time, along with the EVB. Due to the 5G mmWave high frequency and sensitivity, the response of the EVB could be a variable that affects the testing result. When the data is problematic, failure analysis is required to clarify whether the problem is caused by the module itself or by the interference from the EVB. To ensure that the failure analysis is conducted in an efficient way focusing entirely on the module, USI has simplified the test by replacing the EVB with a socket board. As such, the performance testing of the module can be carried out before and after without changing the testing station, which allows us to compare the overall data and eliminate all confounding factors of the testing environment, providing customers with more objective testing information as a reference to adjust the product design.
The functions of monitoring software have also been designed under thoughtful consideration to capture all the details in the testing process. By the matching mechanism of the software and the hardware indicator light, testing engineers can rapidly place the module in its corresponding position, helping to prevent inaccurate testing results from human errors during operations. During the testing process, the system also gives different levels of warnings instructing the testing crew to check the warnings straightforward and solve the problems.
After the reliability testing phase, the modules are sent to the production line for functional testing. The modules are removed from the sockets and directly sent to ATE (Automatic Test Equipment) stations. This method helps the company to reduce functional testing time as well as save additional testing equipment.
Increase the Testing Efficiency
When 5G modules are under high temperature and humidity conditions for reliability testing, the DUT must work and switch to multiple modes. Any issues occurring during the testing process may have resulted from the computer that controls the process, RF cable, different control panels, environmental equipment, or the tested module itself. Therefore, continuously optimizing the system is an important part of the process so that sufficient information will help engineers determine the cause of the error. It will allow to carry out analysis and repair procedures to increase the testing efficiency further.
If a condition cannot be eliminated during the testing process, the test must be stopped and thoroughly overhauled before resuming. As it usually takes 8 to 12 hours at a time, this will significantly impact the overall project timeline. The software is also designed to automatically recover from an abnormality by real-time monitor and directly activating the recovery function. It proactively prevents overhauling caused by abnormal modules, as such the normal modules will not be affected, and there is no need for frequent inspections. It has dramatically improved time efficiency and achieved customers’ expectations in terms of time management.
With our experience in system module testing, USI now offers an automatic testing system with increased testing efficiency for 5G mmWave modules. Also, USI further established a system architecture for RF component reliability testing. We can apply this flexible software to the future tests of other 5G module products. USI’s 5G mmWave module reliability testing system can save up to 85% of setup time and reduce the workforce required to one third or less to meet customers’ need for early transition to mass production.
Keep up with top trending topic
For the latest innovation technology, application
and industry insight.
Subscribe Our Blog
For the latest innovation technology, application
and industry insight.
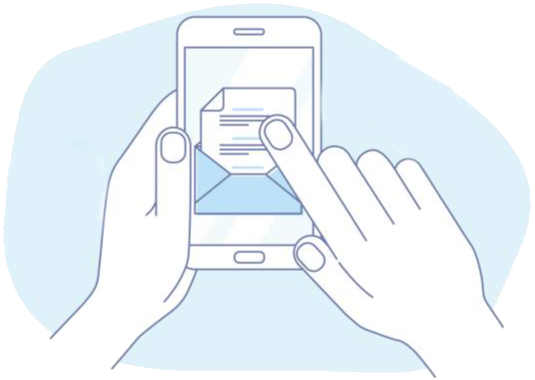