Search
- 03/01/2022
Case Study| USI Developed Dual Robot Test Common Platform to Increase Productivity in 50%
To make production capacity more efficiency to meet customer demand, USI's smart manufacturing department has developed a dual robot test platform incorporating the mechanism design, component selection and software program development of the equipment to replace the original equipment manufacturers’ standard products.
In the dual robot test common platform development, we encountered and tackled various problems, such as feed trays with extensive deformities and irregularities, varying operating heights at various material feed points of the robot arm at each feed tray and feed tray misplacement rates of up to 0.1%. After several discussions, the smart manufacturing team decided to introduce Bézier surface fittings to enable the robot arms to be adapted to the tray at each material feed point. It means that compensation is made for the material placement heights of the arms according to the deformations of the feed tray itself to minimize the. After optimization, the rate was reduced from 0.1% to 0.03%, reaching the standard of 500dppm. This test platform features two highlights:
Highlight 1: Improving output and saving load/unload time
Combining two arms with three suction nozzles to speed up the pick-and-place cycle pace has led to an additional 50% output. Materials can be fed and released stacked instead of loading materials in a single tray. The operator can load 50 feed trays at one time and the trays can be distributed automatically to reduce feed times, saving labor by 33%. In addition, a tray recirculation line has been employed to facilitate automatic tray recycling. Moreover, docking with an Auto Guide Vehicle (AGV) has realized the automatic loading and unloading of the test platform, improving the automation rate.
Highlight 2: One-key correction with built-in ADC to handle production in real-time
The dual robot test common platform is equipped with a Charge Coupled Device (CCD) to realize automatic visual positioning correction and ensure that the arms can accurately pick and place products. A new code-reading function has been built into the tooling to identify whether the product is positioned in the wrong direction or side. The test platform point calibration can be done automatically with just one click, overturning the original way of manual calibration with a pointer. At the same time, the team has developed the Automated Data Collection (ADC) system for the test platform to directly tabulate and visualize the data from hundreds of testing platforms, and enable the operator to quickly understand the production status of the test platform, thereby optimizing timely production capacity.
In general, the design concepts behind USI's self-designed dual robot test common platform can be extended to other similar test platforms in terms of its automation, thus boosting the move toward full-scale intelligent manufacturing.
Keep up with top trending topic
For the latest innovation technology, application
and industry insight.
Subscribe Our Blog
For the latest innovation technology, application
and industry insight.
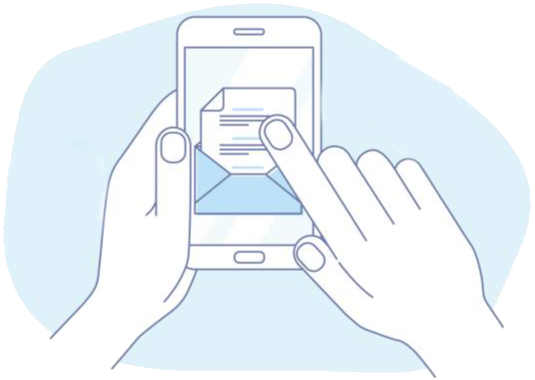