Search
- 01/10/2022
Case Study | How USI Use Automation and Digitalization to Improve High Yield of SiP Module
When the electronics product is getting lighter and thinner, all components are required to be as small as possible, and SiP is one of the technologies that can realize it. To reduce the interference of electromagnetic waves, the sputtering process was introduced. During the manufacturing process of the SiP module, both stainless steel and copper will be utilized in the sputtering process. However, the sputtering process will produce the metal burrs and cause product defection.
Besides its bottom, when carrying out the sputtering process, 5-side of the module will go through the sputtering process. Either Staff or auto-machine will place the module on a sputter carrier with double-sided tape and press-fit it into the machine for magnetic-controlled sputtering. When moving the module from the carrier, it’s common to have the metal burrs on the bottom and sides after the process is complete. These metal burrs would cause product short circuit.
There is 90% product defection from the metal burrs. It’s impossible to have zero metal burrs in the current manufacturing process. Therefore, the most critical mission for the USI R&D team is to find an excellent, efficient method to de-burr and provide a stable and high-quality product.
Introduce De-Burr Automation
In 2015, we used a large workforce by using high-powered microscopic and dust-free cloth wipers to examine and clean the metal burrs. It consumed a lot of time and workforce and tended to result in omissions. After that, the USI engineering team designed a semi-auto de-burr machine. Staff would place the module in the carrier, put a steel net on it to stabilise it, and then use a semi-automatic de-burr machine to brush metal burrs off. Later on, the machine was improved to adapt a vacuum to hold the module instead of putting the steel net and brushing it directly. In 2018, a fully automatic de-burr machine was finally developed and launched.
In 2015, we used a large workforce by using high-powered microscopic and dust-free cloth wipers to examine and clean the metal burrs. It consumed a lot of time and workforce and tended to result in omissions. After that, the USI engineering team designed a semi-auto de-burr machine. Staff would place the module in the carrier, put a steel net on it to stabilise it, and then use a semi-automatic de-burr machine to brush metal burrs off. Later on, the machine was improved to adopt a vacuum to hold the module instead of putting the steel net and brushing it directly. In 2018, a fully automatic de-burr machine was finally developed and launched by the USI engineering team.
Utilize Big Data to Optimize Manufacturing Process
The de-burring process cannot save the root cause. When more metal burrs, more efforts need to be put on. Therefore, the best solution is to reduce the burr ratio from its source by now. From the de-burr data analysis, we discovered that the material quality is related to de-burr efficiency. By analyzing data before and after de-burring, and the forms of metal burrs, we have developed a better double-sided tape material with our suppliers. After introducing this new material, the burr ratio received a significant improvement. Now, the burr ratio before de-burring can be controlled within 5% and even within 100DPPM.
By connecting materials and the system and establishing a pre-and post-manufacturing process feedback system to monitor the usage of brushes and trace the quality records, we can adjust materials and configurations according to data feedback and collect defection records in time. Moreover, we could further carry out research on mechanism models, solve manufacturing process problems, ensure a positive cycle, and improve product qualities.
Currently, in USI, the manufacturing process of module products has been fully automatized. We strive to provide module products of high quality with high efficiency and a high-quality automatic de-burr manufacturing process.
Keep up with top trending topic
For the latest innovation technology, application
and industry insight.
Subscribe Our Blog
For the latest innovation technology, application
and industry insight.
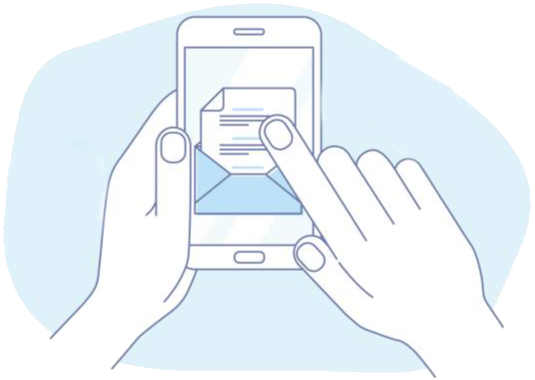