Search
- 04/16/2024
Choosing the Right Path for Advanced Packaging
Developing innovative and high-performance applications often relies on miniaturization technology. Choosing a suitable advanced packaging solution, like System-in-Package (SiP) or System-on-Chip (SoC), is crucial for achieving these goals. Therefore, knowing the key factors that influence packaging selection empowers you to make an informed decision based on your project demands.
1. Understanding Product Requirements
2. Cost Considerations: Balancing Development, Manufacturing, and Components
Development costs significantly impact project feasibility. SoC technology and advanced packaging solutions like CoWoS (Chip-on-Wafer-on-Substrate) often involve complex design and fabrication processes, leading to higher upfront investments. SiP presents a more cost-effective approach. SiP leverages readily available pre-packaged components, minimizing development time and associated costs.
Manufacturing costs also play an important role. SoC technology is a wafer-level process, so the equipment and technology requirements are more complex and more expensive to conduct the production. In contrast, SiP relies on established electric assembly processes, making its manufacturing more cost-effective. Component costs add another layer of complexity. While SoC module potentially offers some cost advantages by integrating functionalities onto a single chip, they may require specialized fabrication processes for non-standard components, potentially negating the initial cost benefit.
3. Time-to-Market: Expediting Product Launch
Development speed is crucial in today's fast-paced tech landscape. SiP technology offers a significant advantage, boasting a much faster development cycle compared to SoC. Utilizing readiness components allows for quicker integration and design cycle time, which reduces the time from conceptualization to product launch. Similarly, SiP technology typically has shorter manufacturing lead times due to established assembly processes.
The Bottom Line: Striking the Perfect Balance
Choosing the suitable packaging solution requires careful consideration of product-specific demands—functionality, size constraints, cost-effectiveness, and time to market. To be frank, there's no one-size-fits-all answer. SiP technology is a champion for compact, feature-rich gadgets, while SoCs reign supreme for processing-intensive products. By understanding these factors, you can make an informed decision about the packaging solution that best transforms the concept into a market-ready reality.
Challenges and Future Trends in SiP Manufacturing
Despite its advantages, SiP manufacturing faces challenges:
Embrace all the Potential with a Trusted Partner
SiP technology offers a powerful solution for miniaturized, high-performance electronics. But navigating the complexities of SiP module design, manufacturing, and integration requires a partner with proven expertise. USI has the capability to realize your imagination in products. We commit to innovation and offer you:
SiP Technology FAQs
1. What is System in Package (SiP)?
System-in-Package (SiP) is a type of advanced packaging technology that integrates multiple components, such as processors, memory, and sensors, into a single module. SiP technology offers several advantages, including reduced size, improved performance, and lower costs.
2. What types of components can be integrated into a SiP?
SiP modules offer high flexibility, allowing the inclusion of processors, memory, sensors, passive components, and even MEMS devices in a single module.
3. Is SiP a cost-effective solution?
SiP technology offers a balance between cost and functionality. While generally more expensive than traditional PCBA, it is more cost-effective than SoCs and Chiplet due to the use of readiness components.
4. What are some applications of SiP technology?
SiP finds applications in various sectors, especially in the areas which require miniaturization, including:
5. What are the specific advantages of using SiP technology in electronic devices?
SiP offers several benefits beyond just size reduction:
6. Where can I learn more about SiP technology and its applications?
Numerous resources are available online, including industry publications, technical articles from reputable sources and educational resources offered by universities and research institutions.
You can start your journey from here in USI Blog:
1. Understanding Product Requirements
The primary consideration should be the product's functionality. SiP technology excels at integrating diverse components—processors, memory, sensors—making it ideal for applications demanding a rich feature set in a compact space. For instance, fitness trackers leverage SiP technology to combine heart rate monitoring, GPS tracking, and sleep analysis functionalities.
On the other hand, products which prioritize raw processing power would benefit from SoC technology. Smartphones that seamlessly run demanding software and graphics-intensive games often utilize SoC modules. This solution integrates the entire processing unit onto a single chip, it could achieve peak performance with tight integration.
However, size constraints must also be factored in. While SoC modules boast the smallest footprint, they may not be suitable for products requiring additional discrete components, such as specialized sensors or extra memory. SiP module then offer a middle ground, striking a balance between miniaturization and the ability to integrate various components.
2. Cost Considerations: Balancing Development, Manufacturing, and Components
Development costs significantly impact project feasibility. SoC technology and advanced packaging solutions like CoWoS (Chip-on-Wafer-on-Substrate) often involve complex design and fabrication processes, leading to higher upfront investments. SiP presents a more cost-effective approach. SiP leverages readily available pre-packaged components, minimizing development time and associated costs.
Manufacturing costs also play an important role. SoC technology is a wafer-level process, so the equipment and technology requirements are more complex and more expensive to conduct the production. In contrast, SiP relies on established electric assembly processes, making its manufacturing more cost-effective. Component costs add another layer of complexity. While SoC module potentially offers some cost advantages by integrating functionalities onto a single chip, they may require specialized fabrication processes for non-standard components, potentially negating the initial cost benefit.
3. Time-to-Market: Expediting Product Launch
Development speed is crucial in today's fast-paced tech landscape. SiP technology offers a significant advantage, boasting a much faster development cycle compared to SoC. Utilizing readiness components allows for quicker integration and design cycle time, which reduces the time from conceptualization to product launch. Similarly, SiP technology typically has shorter manufacturing lead times due to established assembly processes.
The Bottom Line: Striking the Perfect Balance
Choosing the suitable packaging solution requires careful consideration of product-specific demands—functionality, size constraints, cost-effectiveness, and time to market. To be frank, there's no one-size-fits-all answer. SiP technology is a champion for compact, feature-rich gadgets, while SoCs reign supreme for processing-intensive products. By understanding these factors, you can make an informed decision about the packaging solution that best transforms the concept into a market-ready reality.
Challenges and Future Trends in SiP Manufacturing
Despite its advantages, SiP manufacturing faces challenges:
- Increasing component miniaturization and density necessitate advancements in assembly and interconnection techniques.
- Ensuring reliable electrical performance and thermal management becomes more critical with higher component density.
- Continued miniaturization: Advancements in materials science and manufacturing processes will enable even smaller and denser SiP designs.
- Integration of heterogeneous components: SiP will see the incorporation of a wider range of components, including MEMS sensors, power management ICs, and even radio frequency (RF) modules.
- Standardization and Design Automation: Industry efforts towards standardization and design automation tools will streamline SiP development and reduce costs.
Embrace all the Potential with a Trusted Partner
SiP technology offers a powerful solution for miniaturized, high-performance electronics. But navigating the complexities of SiP module design, manufacturing, and integration requires a partner with proven expertise. USI has the capability to realize your imagination in products. We commit to innovation and offer you:
- Diversified Manufacturing Experience: We leverage cutting-edge SiP assembly lines, rigorous quality control processes, and rich manufacturing experiences in diverse products to deliver reliable, high-performing SiP modules.
- Extensive Design Expertise: Our experienced engineering team provides comprehensive support, from SiP design optimization to material selection and testing strategies.
- Seamless Integration: With the advantage of heterogeneous integration, we collaborate closely with customers to ensure smooth integration between different functions, suppliers, and even raw materials, minimizing development time and maximizing efficiency.
- With USI, you have a trusted partner who transforms your vision into reality and empowers your next-generation devices.
SiP Technology FAQs
1. What is System in Package (SiP)?
System-in-Package (SiP) is a type of advanced packaging technology that integrates multiple components, such as processors, memory, and sensors, into a single module. SiP technology offers several advantages, including reduced size, improved performance, and lower costs.
2. What types of components can be integrated into a SiP?
SiP modules offer high flexibility, allowing the inclusion of processors, memory, sensors, passive components, and even MEMS devices in a single module.
3. Is SiP a cost-effective solution?
SiP technology offers a balance between cost and functionality. While generally more expensive than traditional PCBA, it is more cost-effective than SoCs and Chiplet due to the use of readiness components.
4. What are some applications of SiP technology?
SiP finds applications in various sectors, especially in the areas which require miniaturization, including:
- Wearable electronics (smartwatches, fitness trackers)
- Smartphones and mobile devices
- Internet of Things (IoT) devices
- Medical devices (hearing aids, pacemakers)
- Automotive electronics
- Consumer electronics (cameras, drones)
5. What are the specific advantages of using SiP technology in electronic devices?
SiP offers several benefits beyond just size reduction:
- Enhanced Performance: Shortening electrical paths within the SiP module can lead to faster signal transmission and improved overall device performance.
- Greater Design Flexibility: SiP enables the incorporation of various readiness components, catering to diverse functionalities.
- Increased Reliability: The encapsulation protects components from external contaminants and minimizes potential failure sites.
- Faster Time-to-Market: By integrating components early in the design process, SiP can shorten development time to bring a product faster to market.
6. Where can I learn more about SiP technology and its applications?
Numerous resources are available online, including industry publications, technical articles from reputable sources and educational resources offered by universities and research institutions.
You can start your journey from here in USI Blog:
- System in Package (SiP) for Miniaturization: Turnkey Solution We Offer
- Automotive SiP Module: Paving the Way for the Smart Cockpit Revolution
- Mobile Tech is shaping the future of “Connected Health”
- Innovations that Unlock the Potential of Healthcare Technology
- Getting more in less with SiP Ep.3: Miniaturization in Every Details of Your Life
- Getting more in less with SiP Ep.2 : Advanced Packaging Technology on a Miniature Scale
- Getting more in less with SiP Ep.1: Global Trends & Market Demands
Keep up with top trending topic
For the latest innovation technology, application
and industry insight.
Subscribe Our Blog
For the latest innovation technology, application
and industry insight.
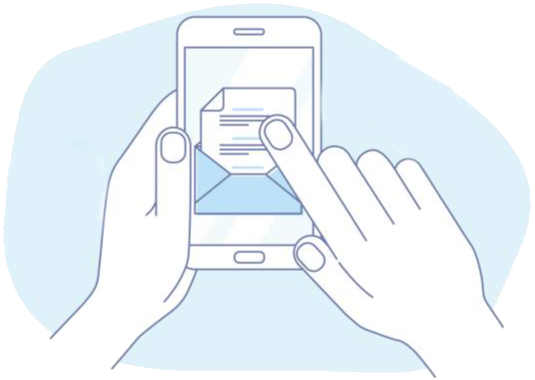